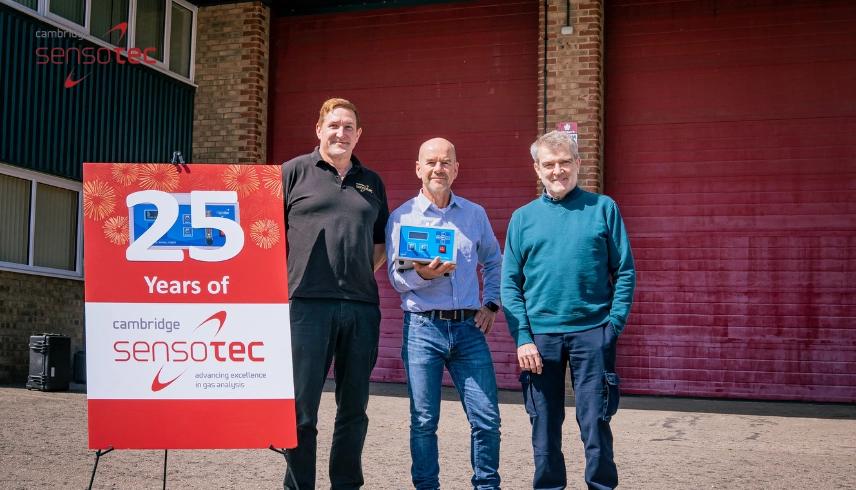

Ensuring Material Integrity: Gas Detection Technologies in Metal 3D Printing
Introduction:
Metal 3D printing, also known as additive manufacturing, has revolutionised various industries by enabling the production of complex and customised metal parts with unprecedented precision. However, ensuring the integrity and quality of printed components remains a critical challenge. Gas detection technologies offer a solution to this challenge, providing valuable insights into the printing process and enhancing material integrity. In this blog post, we explore the importance of gas detection technologies in metal 3D printing and their role in ensuring the reliability of printed parts.
Understanding Gas Detection in Metal 3D Printing:
Gas detection in metal 3D printing involves the analysis of gases emitted during the printing process. These gases can originate from various sources, including the metal powder, printing environment, and interaction between the metal and the printing medium. By monitoring and analysing these gases, manufacturers can gain valuable insights into the printing process and identify potential issues that may affect material integrity.
Importance of Gas Detection for Material Integrity:
Gas detection technologies play a crucial role in maintaining material integrity throughout the metal 3D printing process. They help identify and mitigate issues such as porosity, contamination, and improper fusion, which can compromise the mechanical properties and structural integrity of printed parts. By detecting and addressing these issues in real-time, manufacturers can ensure the quality and reliability of their printed components.
Types of Gas Detection Technologies:
Several gas detection technologies are commonly used in metal 3D printing, including optical emission spectroscopy (OES), laser-induced breakdown spectroscopy (LIBS), and residual gas analysis (RGA). These technologies offer different capabilities and sensitivities, allowing manufacturers to choose the most suitable option for their specific application. Additionally, advanced gas detection systems may incorporate sensors and monitoring devices directly into the printing equipment for seamless integration and real-time monitoring.
Benefits of Gas Detection in Metal 3D Printing:
The integration of gas detection technologies into metal 3D printing processes offers numerous benefits, including:
- Enhanced material integrity and reliability of printed parts
- Early detection of printing issues and defects
- Improved process control and optimisation
- Reduced scrap and rework rates
- Compliance with industry standards and quality requirements
Conclusion:
Gas detection technologies play a critical role in ensuring the material integrity and reliability of metal 3D printed parts. By monitoring and analysing gases emitted during the printing process, manufacturers can identify and address issues that may compromise the quality of printed components. Cambridge Sensotec offers advanced gas detection solutions designed to meet the unique needs of metal 3D printing applications. Contact us today to learn more about our products and how they can enhance the quality and reliability of your printed parts.
Further Reading:
- Gas Detection in Metal Printing: Exploring the Importance and Applications
- Oxygen Depletion in Metal Printing: Ensuring Material Integrity
- How Gas Analysis Optimizes Metal 3D Printing Results: A Comprehensive Guide
Explore more insights and resources on gas detection technologies and their applications in metal 3D printing to enhance your understanding and optimise your processes. Ready to take the next step in improving your metal 3D printing operations? Contact us today to discuss your specific needs and discover how Cambridge Sensotec can assist you!