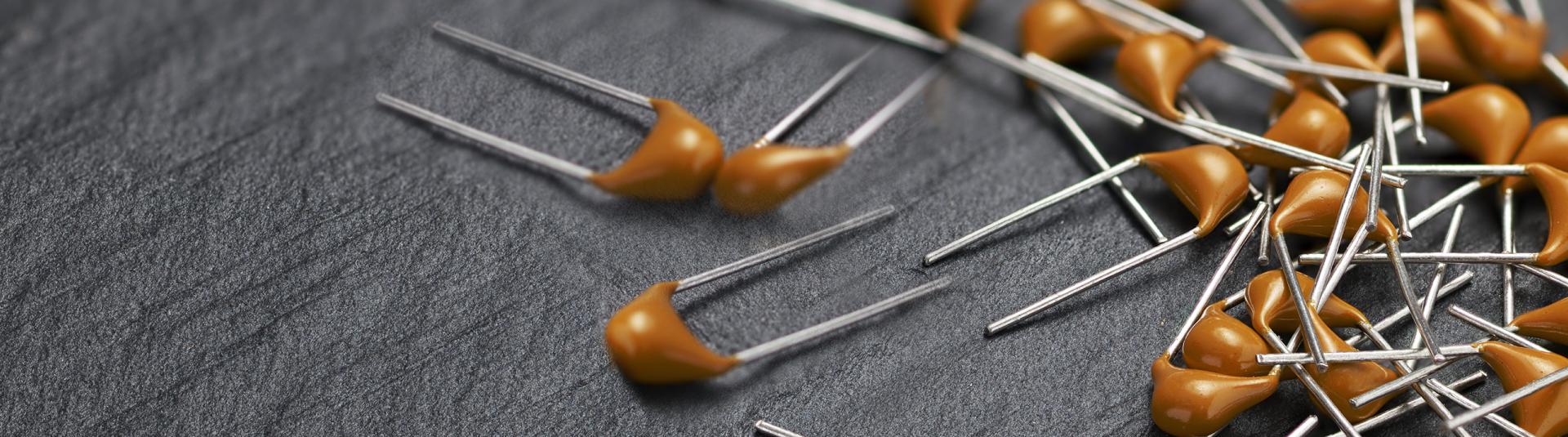
Ceramic Capacitors
The presence of both precious metal electrodes and ceramic layers which are ultra-thin, means that MLCC’s need to be sintered in very controlled atmospheres to prevent oxidation damage to the precious metals used in the conductive layers.
By employing oxygen (O2) gas analysis to measure the performance of the forming gas directly in the oven itself, engineers can control the atmosphere in the oven very accurately to give the correct oxygen partial pressure, which allows the metal layers to remain conductive whilst baking the ceramic layers to the required density for the required capacitance value. Only by doing this can the product be mass produced with the same electrical properties time and time again.
Another primary reason gas analysis is crucial in ceramic capacitors is the identification and analysis of outgassing gases produced as the organic binders decompose. Outgassing refers to the release of volatile compounds from the materials used in the construction of ceramic capacitors.
By conducting gas analysis, engineers can identify the specific outgassing gases and their concentrations. This knowledge helps in understanding the impact of outgassing on capacitance, impedance, and overall performance, allowing for the optimisation of materials and manufacturing processes to reduce or eliminate the detrimental effects of outgassing. It also helps to optimise the furnace heating and cooling profile to maximise performance yet minimise energy consumption.
Reactive gases pose another challenge in performance. Gases such as moisture and oxygen can react with the materials used in capacitors, leading to chemical reactions and degradation of the dielectric properties. Gas analysis allows for the detection and quantification of reactive gases within ceramic capacitors. By understanding the types, concentrations, and sources of reactive gases, engineers can develop strategies to mitigate their influence. This may involve the selection of suitable materials, improved sealing techniques, and the implementation of protective coatings to prevent or minimise the interaction between reactive gases and the capacitor components.
Product Filters
Showing all 7 results
-
Rapidox 1100 Oxygen Analyser
Number of Gases 1 Sensor Option Internal -
Rapidox 1100 Carbon Dioxide Gas Analyser
Number of Gases 1 Sensor Option Internal -
Rapidox 1100 Carbon Monoxide Analyser
Number of Gases 1 Sensor Option Internal -
Rapidox 1100 Helium Analyser
Number of Gases 1 Sensor Option Internal -
Rapidox 1100 Methane Analyser
Number of Gases 1 Sensor Option Internal -
Rapidox 2100 OEM-SIL2
Number of Gases 1 Sensor Option Remote -
Rapidox 2100-OEM-RSB-INS and ENC
Number of Gases 1 Sensor Option Remote
Showing all 7 results