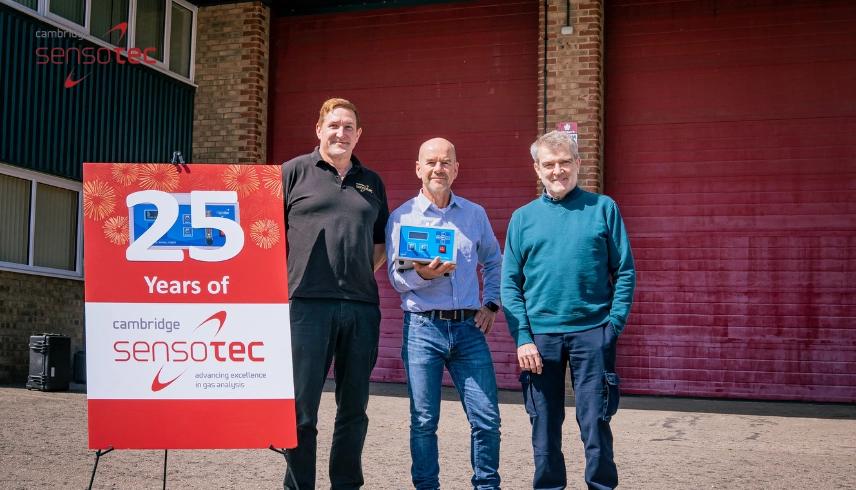
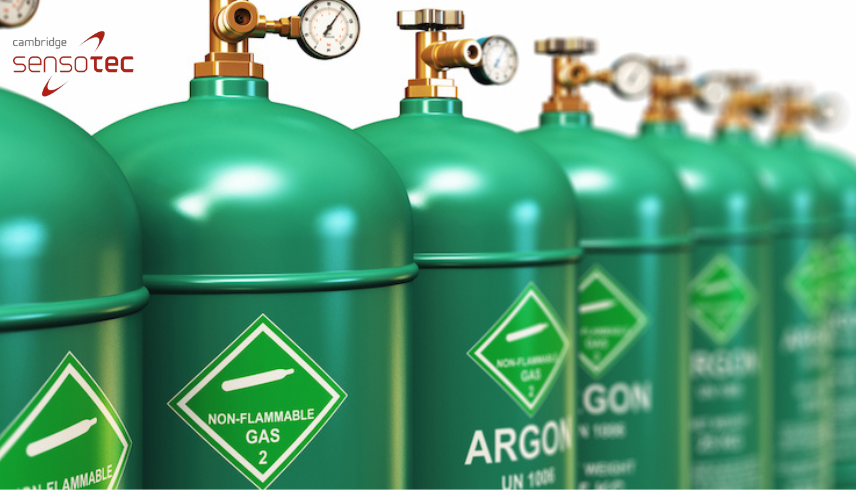
Enhancing Performance with Argon Gas for MIG Welding
In the world of welding, the choice of shielding gas plays a pivotal role in determining the quality and efficiency of the weld. Argon gas is a popular choice for MIG (Metal Inert Gas) welding, known for its superior properties that enhance weld performance. At Cambridge Sensotec, we specialise in advanced gas analysis solutions that help optimise the use of argon gas in MIG welding. Here’s an in-depth look at how to maximise the benefits of argon gas for MIG welding.
The Role of Argon Gas in MIG Welding
MIG welding, also known as Gas Metal Arc Welding (GMAW), involves the use of a continuous wire electrode and a shielding gas to protect the weld pool from atmospheric contamination. Argon, an inert gas, is commonly used as a shielding gas due to its excellent arc stability and protective properties.
Benefits of Using Argon Gas for MIG Welding
1. Superior Arc Stability
Argon provides a stable arc, which is crucial for producing consistent and high-quality welds. The stability of the arc helps maintain a smooth and controlled weld pool, reducing the likelihood of defects and rework.
2. Cleaner Welds
Using argon gas results in cleaner welds with minimal spatter and oxidation. This is especially important when welding materials like aluminium and stainless steel, where cleanliness and precision are paramount.
3. Enhanced Weld Appearance
Argon gas produces aesthetically pleasing welds with smooth, uniform beads. The inert atmosphere created by argon prevents contamination and oxidation, ensuring a polished and professional finish.
4. Versatility
Argon is suitable for welding a wide range of metals, including aluminium, stainless steel, copper, and magnesium. Its versatility makes it a preferred choice across different industries that work with diverse materials.
5. Improved Penetration
Argon gas helps achieve deeper penetration in the weld, which is essential for ensuring strong and durable joints. This is particularly beneficial in applications requiring high-strength welds.
Optimising Argon Gas for MIG Welding: Key Strategies
1. Use High-Purity Argon
The purity of argon gas directly impacts the quality of the weld. Using high-purity argon ensures that the shielding gas is free from contaminants that could compromise the weld integrity. Cambridge Sensotec offers advanced gas analysers to monitor and maintain the purity of argon gas.
2. Correct Gas Flow Rate
Setting the correct gas flow rate is crucial for effective shielding. Too high a flow rate can cause turbulence and introduce contaminants, while too low a flow rate may not provide adequate protection. Typically, a flow rate of 15-20 cubic feet per hour (CFH) is recommended for MIG welding.
3. Regular Equipment Maintenance
Ensure that your MIG welding equipment, including gas regulators, hoses, and torches, is well-maintained and free from leaks. Regular maintenance helps maintain consistent gas flow and prevents contamination.
4. Monitor Gas Usage
Implementing advanced gas analysers, such as those provided by Cambridge Sensotec, allows for real-time monitoring of gas flow and concentration. This helps optimise gas usage, reduce waste, and ensure consistent shielding throughout the welding process.
5. Proper Welding Techniques
Training and educating welders on proper techniques, such as maintaining the correct torch angle and distance, are crucial for optimising the use of argon gas. Proper technique ensures effective shielding and high-quality welds.
Cambridge Sensotec’s Advanced Gas Analysis Solutions
At Cambridge Sensotec, we offer state-of-the-art gas analysis solutions designed to help you optimise your MIG welding processes. Our Rapidox gas analysers provide accurate, real-time data on gas purity and flow rates, enabling you to make informed decisions and achieve superior welding results.
Benefits of Our Gas Analysis Solutions
- Precision Monitoring: Ensure high-purity argon gas with precise monitoring of gas composition.
- Real-Time Data: Access real-time data on gas flow rates and concentrations.
- Enhanced Efficiency: Optimise gas usage and reduce waste with accurate monitoring.
- Comprehensive Support: Receive expert support and training to maximise the benefits of our gas analysis solutions.
Conclusion
Optimising argon gas for MIG welding is essential for achieving superior weld quality, precision, and efficiency. By using high-purity argon, maintaining proper gas flow rates, and implementing advanced gas analysis solutions from Cambridge Sensotec, you can enhance your welding processes and produce exceptional results.
Visit our website or contact us to learn more about our advanced gas analysis solutions and how we can help you optimise your MIG welding applications. Discover the difference that precise gas management can make in your welding outcomes.