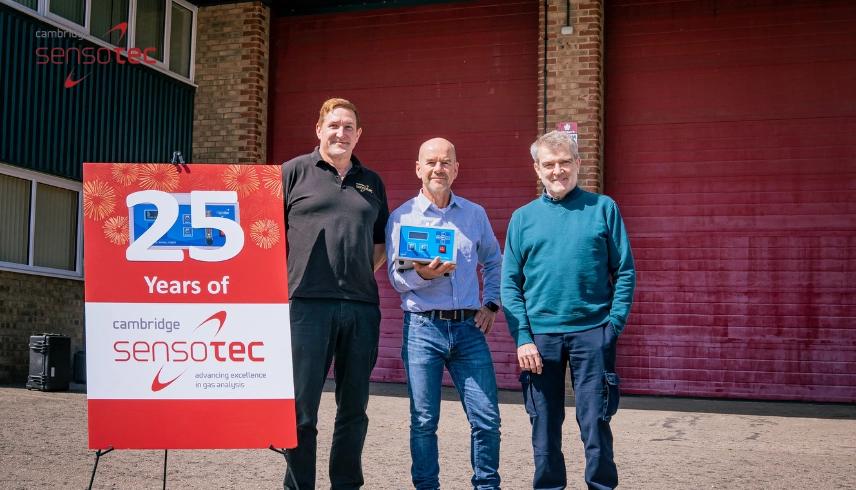
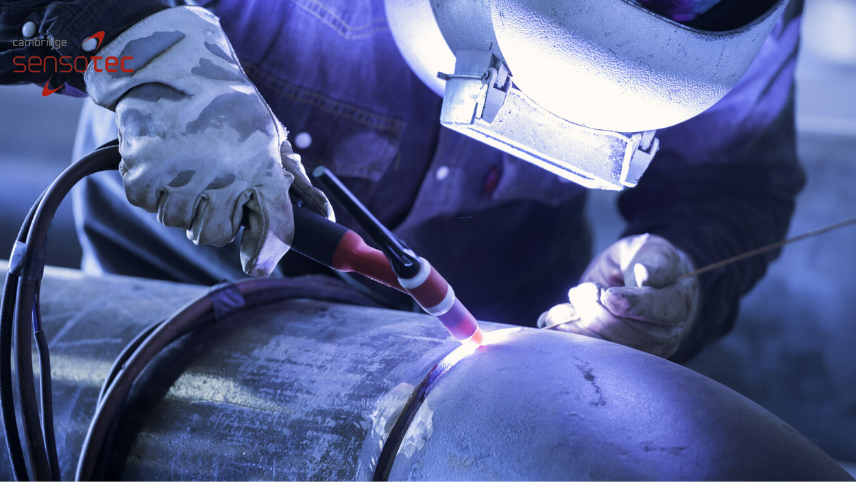
Optimising Argon Welding Gas for Superior Results
Argon welding is a widely used technique in various industries due to its numerous benefits, such as high-quality welds and excellent precision. However, optimising the use of argon gas in welding is crucial to achieving superior results. At Cambridge Sensotec, we provide advanced gas analysis solutions to help you optimise your argon welding processes. Here’s how you can enhance your welding outcomes by effectively managing argon gas.
Understanding the Role of Argon in Welding
Argon is an inert gas, meaning it does not react with other elements. This property makes it ideal for welding applications, particularly in Gas Tungsten Arc Welding (GTAW) or Tungsten Inert Gas (TIG) welding and Gas Metal Arc Welding (GMAW) or Metal Inert Gas (MIG) welding. Argon creates a protective atmosphere around the weld, preventing oxidation and contamination, which are crucial for producing clean and strong welds.
Benefits of Using Argon in Welding
Enhanced Weld Quality
Argon provides a stable shielding environment that protects the molten metal from atmospheric contaminants like oxygen, nitrogen, and hydrogen. This results in high-quality welds with minimal defects such as porosity and brittleness.
Improved Precision and Control
Using argon allows for greater control over the welding process, making it ideal for applications that require precision, such as in the aerospace and electronics industries. The inert nature of argon ensures a consistent arc and smooth weld pool.
Versatility
Argon is suitable for welding a variety of metals, including aluminium, stainless steel, copper, and magnesium. This versatility makes it a preferred choice across different industries that work with diverse materials.
Better Aesthetic Finish
Argon welding produces cleaner welds with fewer spatters and less oxidation. This results in a smoother finish that often requires minimal post-weld cleaning and polishing.
Enhanced Arc Stability
Argon’s properties provide excellent arc stability, ensuring even heat distribution and penetration. This reduces the likelihood of weld defects and the need for rework.
Optimising Argon Welding Gas: Key Strategies
1. Use High-Purity Argon
Using high-purity argon gas is essential for achieving superior weld quality. Impurities in the gas can lead to contamination and defects in the weld. Ensure that your argon supply is of high purity to maintain the integrity of your welds.
2. Proper Gas Flow Rate
Adjusting the gas flow rate is critical to protecting the weld area and achieving optimal results. Too high a flow rate can cause turbulence and contamination, while too low a flow rate may not provide adequate shielding. Use the recommended flow rates for your specific welding application.
3. Regular Equipment Maintenance
Ensure that your welding equipment, including gas regulators, hoses, and torches, is well-maintained and free from leaks. Regular maintenance helps maintain consistent gas flow and prevents contamination.
4. Monitor Gas Usage
Monitoring gas usage helps optimise consumption and reduce waste. Implementing advanced gas analysers, such as those provided by Cambridge Sensotec, allows for real-time monitoring of gas flow and concentration, ensuring efficient use of argon.
5. Proper Welding Techniques
Proper welding techniques, such as maintaining the correct torch angle and distance, are crucial for optimising argon gas use. Training and educating welders on best practices can significantly improve welding outcomes.
Cambridge Sensotec’s Advanced Gas Analysis Solutions
At Cambridge Sensotec, we offer state-of-the-art gas analysis solutions to help you optimise your argon welding processes. Our Rapidox gas analysers provide accurate, real-time data on gas purity and flow rates, enabling you to make informed decisions and achieve superior welding results.
Benefits of Our Gas Analysis Solutions
- Precision Monitoring: Ensure high-purity argon gas with precise monitoring of gas composition.
- Real-Time Data: Access real-time data on gas flow rates and concentrations.
- Enhanced Efficiency: Optimise gas usage and reduce waste with accurate monitoring.
- Comprehensive Support: Receive expert support and training to maximise the benefits of our gas analysis solutions.
Conclusion
Optimising argon welding gas is essential for achieving superior weld quality, precision, and efficiency. By using high-purity argon, maintaining proper gas flow rates, and implementing advanced gas analysis solutions from Cambridge Sensotec, you can enhance your welding processes and produce exceptional results.
Visit our website or contact us to learn more about our advanced gas analysis solutions and how we can help you optimise your argon welding applications. Discover the difference that precise gas management can make in your welding outcomes.