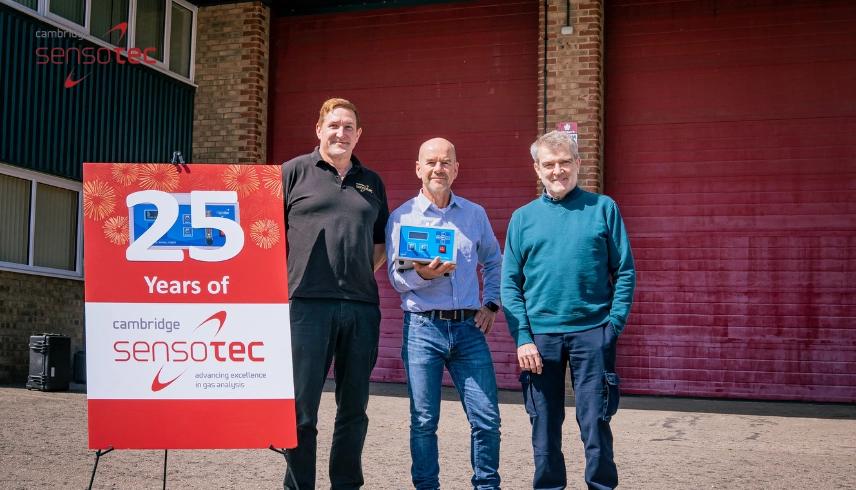
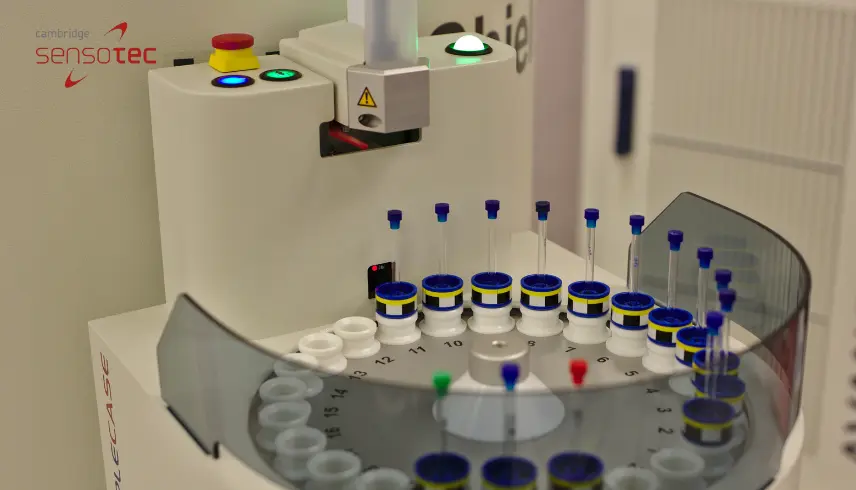
SIL2 Gas Analysers in Pharmaceuticals: Ensuring Process Safety
Introduction
The pharmaceutical industry demands absolute precision, reliability, and safety throughout every stage of production. Whether manufacturing life-saving medicines or performing sensitive research, facilities must maintain strict control over environmental conditions. One often overlooked but essential component is gas analysis. Gases such as oxygen, nitrogen, and carbon dioxide play a vital role in pharmaceutical processes, from fermentation to packaging. As the industry faces stricter regulations and increasing safety standards, the adoption of SIL2 gas analyzers is becoming critical for ensuring process safety and compliance.
What is SIL2 and Why Does it Matter in Pharmaceuticals?
SIL2, or Safety Integrity Level 2, is defined under the IEC 61508 standard. It refers to the functional safety of electrical, electronic, and programmable systems. A SIL2-rated gas analyzer is designed to operate reliably under defined conditions, reducing the risk of system failure that could compromise safety or product quality.
In pharmaceutical settings, even the smallest deviation in gas composition can lead to contamination, product loss, or worse, compromised patient safety. Incorporating SIL2-compliant gas monitoring systems adds a layer of assurance that gases are consistently controlled. This becomes especially important in sterile production environments, fermentation tanks, packaging lines, and inerting operations where fluctuations in oxygen or other gas levels can directly impact outcomes.
For an overview of SIL2 and its broader role across industries, visit our article on Understanding SIL2.
Benefits and Impacts on Process Safety
The advantages of using SIL2 gas analyzers in pharmaceutical applications extend beyond basic compliance. These analyzers enhance operational reliability by delivering accurate, real-time data that ensures safe gas levels are consistently maintained. They play a crucial role in detecting any unexpected changes in flow or composition, helping teams address potential issues before they affect the product.
Real-time fault detection minimises the risk of contamination and supports uninterrupted production. For instance, if a bioreactor requires a precise mix of gases to sustain microbial growth, even slight variations can result in batch failure. A SIL2-certified system allows operators to react immediately, avoiding product waste and downtime.
SIL2 compliance also supports traceability. Pharmaceutical manufacturers need to maintain clear, auditable records to meet GMP (Good Manufacturing Practice) and health authority expectations. Analyzers with SIL2 certification often come equipped with automated logging features, ensuring that every data point is captured and stored securely.
Beyond process control, these systems improve workplace safety. Inerting systems that reduce oxygen concentrations must operate within very specific parameters. SIL2 analyzers provide the reassurance that oxygen levels remain stable, reducing the risk of combustion in sensitive areas.
By offering a consistent safety framework, SIL2-certified systems also standardise risk management across multiple production sites. For multinational pharmaceutical firms, this consistency is crucial for achieving global compliance and operational harmony. The implementation of uniform monitoring systems across different locations also simplifies staff training and maintenance procedures.
Applications in Pharmaceutical Environments
SIL2 gas analyzers are increasingly integrated into cleanrooms to monitor for contaminants or unwanted fluctuations in oxygen concentration. Their role in bioprocessing is also expanding, where they help maintain optimal gas conditions in cell cultures or microbial fermentation tanks.
In lyophilisation (freeze drying), it’s essential to control inert gas levels during drying and sealing to prevent oxidation. SIL2 systems offer the responsiveness needed to adjust gas flow and composition dynamically. Similarly, in modified atmosphere packaging, maintaining exact gas concentrations preserves product efficacy and extends shelf life.
In addition, pharmaceutical companies are using these analyzers in storage and transport to monitor inerting processes. Gas analyzers integrated with safety systems help to immediately detect oxygen ingress or gas leaks, triggering alarms or automatic shutdowns if thresholds are exceeded.
Beyond these applications, SIL2 analyzers support energy optimisation by fine-tuning gas usage, reducing waste and improving environmental sustainability. With carbon footprint reduction becoming a growing priority, these systems help align production with environmental targets. They also reduce dependency on manual gas checks, freeing staff to focus on higher-level operations.
For an example of how SIL2 is reshaping gas monitoring in other high-risk environments, visit our article on SIL2 in Additive Manufacturing.
Meeting Regulatory Demands and Supporting GMP
Maintaining robust documentation and validation is essential for GMP compliance. SIL2 gas analyzers are designed with audit-readiness in mind. With features like secure data logging, timestamped reports, and automated calibration tracking, these tools make it easier to present evidence during inspections.
They also support adherence to international standards like ISO 13485 and 21 CFR Part 11, which focus on electronic records and data integrity. When paired with centralised data systems, SIL2 analyzers become part of a broader digital validation strategy that supports regulatory transparency.
SIL2 analyzers also reduce the risk of non-compliance penalties and improve a facility’s ability to respond to regulatory changes. With continuous updates to regional and international pharmaceutical standards, having a flexible, upgrade-ready system in place is critical.
Enhancing Operational Efficiency and Future Trends
Operational efficiency in pharmaceutical manufacturing hinges on minimising waste and ensuring continuous production. By using SIL2-certified equipment, facilities can detect problems early and avoid costly shutdowns. These analyzers enable teams to take proactive steps based on reliable data, reducing reliance on manual checks.
Future developments in pharmaceutical technology will likely involve greater automation, remote monitoring, and predictive analytics. SIL2 gas analyzers are well-positioned to support these advancements, particularly when integrated with cloud-based platforms and AI-driven control systems. As regulatory expectations evolve, SIL2 technology ensures that safety and data integrity remain at the forefront.
The growing demand for personalised medicine, biologics, and advanced therapeutics will further drive the need for precise gas control. These emerging modalities rely heavily on strict environmental parameters, where SIL2 analyzers provide the accuracy and reliability required. Pharmaceutical facilities that adopt this technology today are better positioned to meet the demands of future innovation.
Conclusion
As the pharmaceutical industry continues to prioritise quality, safety, and compliance, SIL2 gas analyzers offer a vital solution for modern manufacturing environments. From reducing contamination risk to enabling proactive fault detection, these systems provide the functional safety required to support critical operations.
With their ability to improve traceability, support audit readiness, and integrate with smart factory systems, SIL2 analyzers are becoming an indispensable part of pharmaceutical process control.
Cambridge Sensotec delivers advanced gas analysis technology designed to meet SIL2 requirements. Contact us to learn how our solutions can support safety and compliance in your pharmaceutical processes.