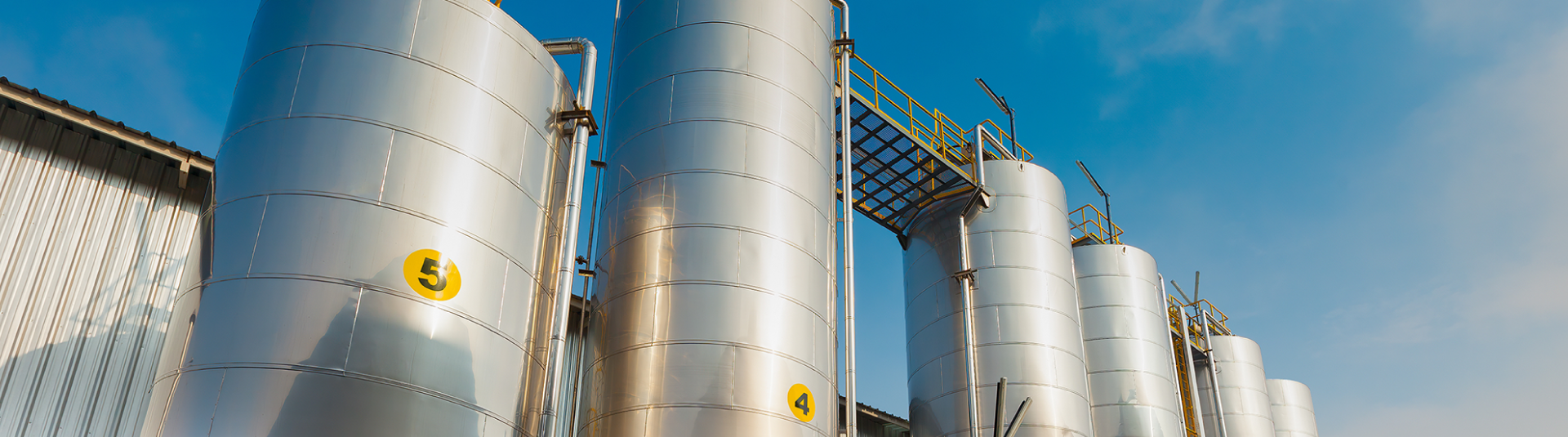
Inert Gas Blanketing
In industries such as oil and gas, chemical manufacturing, and food production, where safety and product integrity are paramount, inert gas blanketing is widely implemented.
By displacing oxygen, inert gas blanketing mitigates the risk of undesirable reactions, such as combustion or oxidation, that can occur when volatile substances come into contact with oxygen. By maintaining an oxygen-free environment, the potential for fires, explosions, or degradation of sensitive materials is significantly reduced.
Inert gas blanketing is particularly crucial for preserving perishable products, such as food and pharmaceuticals, by creating an oxygen-free environment. By eliminating or reducing the presence of oxygen, the growth of spoilage-causing microorganisms is inhibited, extending the shelf life and maintaining the quality and freshness of the products.
Gas analysis plays a critical role in ensuring it’s effectiveness and reliability. By analysing the gas composition and monitoring oxygen levels, gas analysis provides valuable insights into the displacement of oxygen and the purity of the inert gas.
To verify the success of the blanketing process, gas analysis focuses on analysing oxygen levels as an impurity within the inert gas. By measuring the oxygen concentration, engineers can ensure that the oxygen has been adequately displaced and that the inert gas is of sufficient purity. This step is essential to prevent any potential reactions that could occur due to residual oxygen, such as spontaneous combustion or oxidative degradation of the protected materials.
Gas analysis is a vital tool in optimising practices and maintaining the integrity of materials across a range of industries.
Product Filters
Showing all 10 results
-
Rapidox 1100 Oxygen Analyser
Number of Gases 1 Sensor Option Internal -
Rapidox 1100 Carbon Dioxide Gas Analyser
Number of Gases 1 Sensor Option Internal -
Rapidox 1100 Carbon Monoxide Analyser
Number of Gases 1 Sensor Option Internal -
Rapidox 1100 Helium Analyser
Number of Gases 1 Sensor Option Internal -
Rapidox 1100 Methane Analyser
Number of Gases 1 Sensor Option Internal -
Rapidox 2100 Oxygen Analyser
Number of Gases 1 Sensor Option Remote -
Rapidox 2100-OEM-RSB and DIN
Number of Gases 1 Sensor Option Remote -
Rapidox 2100 OEM-SIL2
Number of Gases 1 Sensor Option Remote -
Rapidox 2100-OEM-RSB-INS and ENC
Number of Gases 1 Sensor Option Remote -
Rapidox 3100 Multigas Analyser
Number of Gases Up to 3 Sensor Option Internal
Showing all 10 results